Injection Plastic Molds: Revolutionizing Metal Fabrication
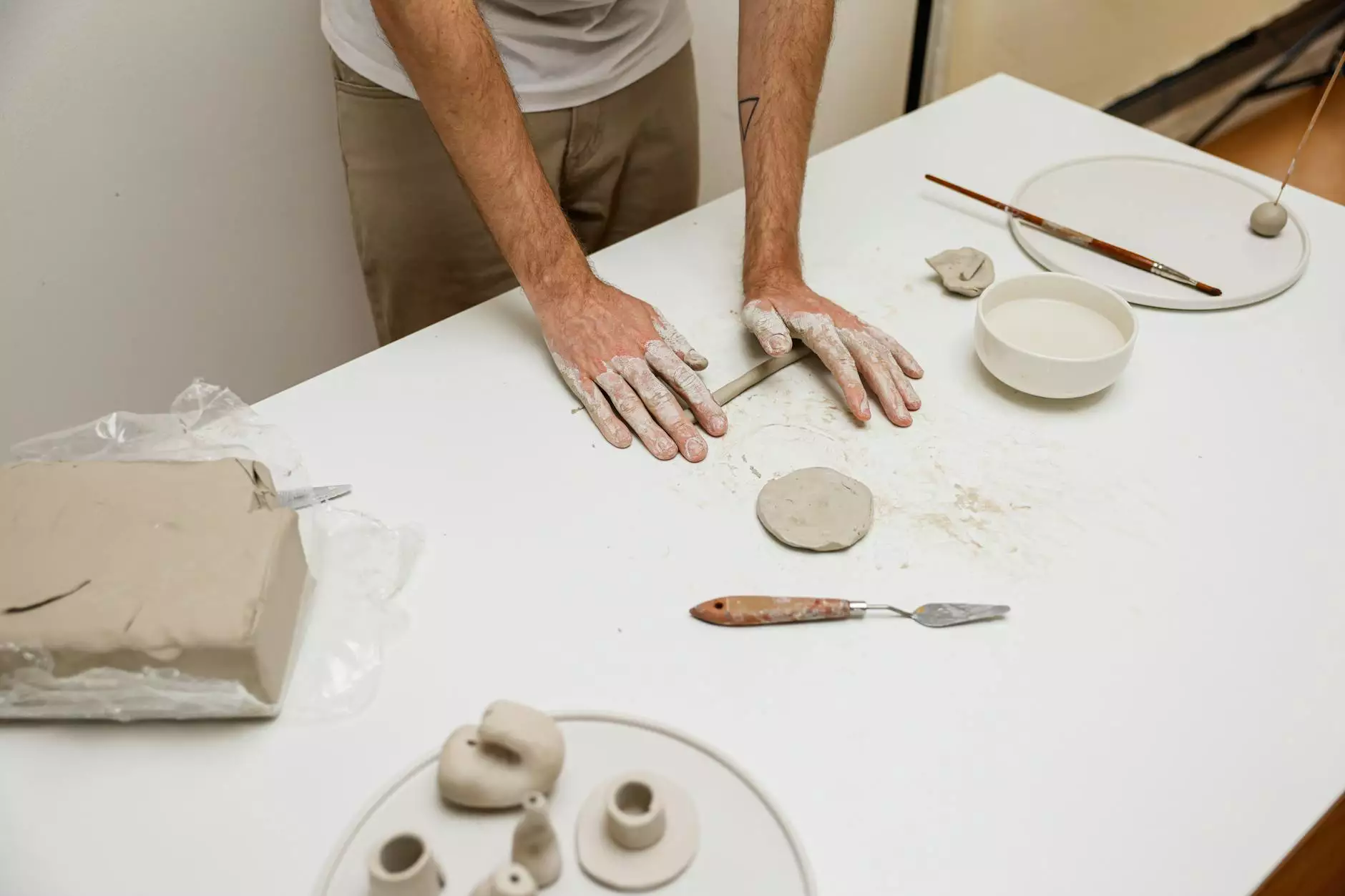
In the modern manufacturing landscape, the injection plastic mold has emerged as a game-changing technology for businesses involved in metal fabrication. This article delves deep into the intricacies of injection molding, its applications, benefits, and its pivotal role in enhancing production efficiency and product quality.
Understanding Injection Molding
To appreciate the superiority of injection plastic molds, it is essential to understand what injection molding entails. This manufacturing process involves injecting molten material into a mold cavity, allowing for the creation of complex and precise parts. Here’s a breakdown of how it works:
- Material Preparation: The process begins with the selection of materials, commonly thermoplastics or thermosetting polymers, which are then heated until they are in a liquid state.
- Injection: The molten plastic is injected into a pre-designed mold under high pressure.
- Cooling: The injected material cools and solidifies within the mold, taking on its shape.
- Mold Opening: Once cooled, the mold opens, and the finished part is ejected.
The Advantages of Injection Plastic Molding
Utilizing injection plastic molds holds numerous advantages for metal fabricators, including:
- High Efficiency: Injection molding is one of the fastest ways to manufacture parts, significantly reducing production time.
- Consistent Quality: The process ensures uniformity in the products, minimizing defects and variations.
- Cost-Effectiveness: Although initial setup costs may be high, per-unit costs decrease with increased production volume, making it economical for large runs.
- Complex Designs: Injection molds can create intricate shapes and designs that would be challenging or impossible with other methods.
- Material Versatility: A wide range of thermoplastics can be used, allowing for flexibility in product design.
Applications of Injection Plastic Molds in Metal Fabrication
The integration of injection plastic molds into metal fabrication processes opens up a myriad of applications. Here are some notable uses:
1. Automotive Industry
In the automotive sector, injection molded plastics are essential for producing components such as dashboard parts, exterior trims, and under-the-hood components. The ability to shape complex parts that meet stringent safety and aesthetic standards is invaluable.
2. Consumer Electronics
The electronics industry relies on precision-made parts. Injection plastic molds allow for intricate designs necessary for device casings, connectors, and internal components.
3. Medical Devices
In the medical field, injection molding creates high-quality, sterile products such as syringes, surgical instruments, and housings for medical devices, where precision and compliance with regulations are crucial.
4. Packaging Solutions
Injection molding is widely used to produce packaging components more effectively and sustainably, creating both rigid and flexible packaging that meets various market needs.
Choosing the Right Injection Plastic Mold for Your Needs
Selecting the right injection plastic mold involves several considerations that can impact your production outcomes:
1. Mold Material
The choice of mold material (e.g., steel, aluminum) affects durability, cost, and production volume. Steel molds, while more expensive, offer long-term solutions for high-volume production, while aluminum is typically used for short runs.
2. Mold Design
A well-optimized mold design is crucial. It should facilitate efficient material flow, manage cooling rates, and ease part ejection to ensure production efficiency and product quality.
3. Production Volume
Your expected production volume should heavily influence your mold choice. Higher volumes typically justify the higher initial costs of more durable molds.
Best Practices for Injection Molding
To maximize the potential of injection plastic molds, consider these best practices:
- Invest in Quality Molds: Quality molds prevent defects and extend the lifespan of the tooling.
- Optimize Parameters: Fine-tuning injection speed, temperature, and pressure are key to achieving the desired quality and consistency.
- Conduct Regular Maintenance: Routine inspections and maintenance of molds ensure consistent performance and prevent breakdowns.
- Utilize Proper Cooling Techniques: Efficient cooling can significantly shorten cycle times and improve part quality.
The Future of Injection Plastic Molding
The field of manufacturing continues to evolve, and the future of injection plastic molds is no exception. Innovations in materials, sustainability practices, and automation are reshaping the landscape:
1. Eco-friendly Materials
With an increasing emphasis on sustainability, manufacturers are exploring biodegradable plastics and recycled materials, thereby reducing environmental impact.
2. Automation and Industry 4.0
The integration of smart technology and automation in injection molding operations enhances efficiency and error reduction, paving the way for smarter factories.
3. Advanced Design Software
Utilizing advanced CAD and simulation software allows for better mold designs and predictive analysis, optimizing performance before the production stage.
Conclusion
In summary, injection plastic molds are an indispensable component of modern metal fabrication and manufacturing. Their ability to produce high-quality, complex, and consistent parts at scale provides manufacturers with a competitive edge in various industries. As technology advances, the benefits and applications of injection molding will continue to grow, paving the way for innovation and increased productivity in the fabrication landscape.
Manufacturers looking to enhance their operations should consider integrating injection molding into their processes and stay informed about the innovations that emerge in this dynamic field. Visit deepmould.net for more insights and information on partnering with experienced metal fabricators well-versed in injection plastic molding techniques.