Transforming Possibilities: The Role of Precision Injection Molded Plastics in Metal Fabrication
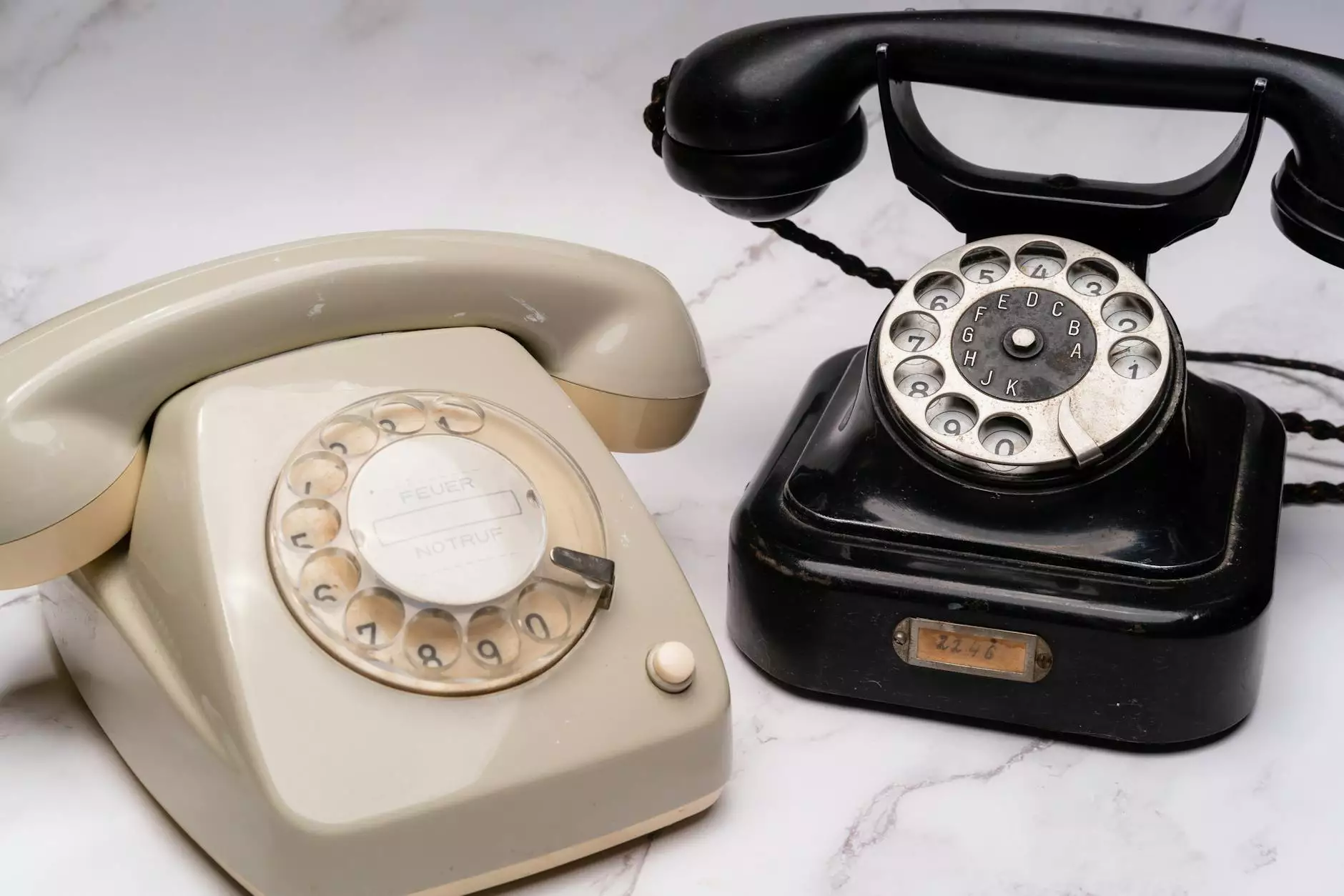
In today’s fast-paced manufacturing world, precision injection molded plastics stand out as a transformative force in the metal fabrication sector. The integration of this advanced technology dramatically influences production efficiency, product quality, and overall competitiveness in various industries. This article delves deep into the multifaceted world of precision injection molded plastics, showcasing their significance in metal fabrication, along with various applications, benefits, and emerging trends.
The Basics of Precision Injection Molding
Precision injection molding is a manufacturing process that involves injecting molten material into a mold to create detailed and complex plastic parts. This technique is not limited to plastic alone; it can also work in conjunction with metals, creating hybrid components that combine the resilience of metal with the lightweight properties of plastics. Here’s a closer look at the fundamental aspects:
- Material Selection: The choice of materials is paramount. Typically, thermoplastics and thermosetting plastics are used, tailored for specific application requirements.
- Mold Design: The design of molds is critical for achieving high precision. Advanced software tools aid in creating intricate designs that meet precise dimensional specifications.
- Process Control: Parameters such as temperature, pressure, and cooling time are meticulously controlled to ensure consistency and quality.
Advantages of Using Precision Injection Molded Plastics
The advantages of implementing precision injection molded plastics in metal fabrication are numerous, making it an attractive option for manufacturers. Here are some compelling reasons:
- Cost Efficiency: The reduced waste during production and the ability to mass produce components lead to cost savings in labor and materials.
- High Precision and Quality: Advanced molding techniques allow for intricate designs with tight tolerances, ensuring high-quality output.
- Versatility: The capability to mold a variety of shapes and sizes enables manufacturers to cater to specific client needs across diverse industries.
- Reduced Weight: Precision molded plastics typically offer a lighter alternative to metal, thus enhancing the performance of products, especially in automotive and aerospace applications.
- Resistance to Corrosion and Chemicals: Plastics provide excellent resistance to corrosive environments, which is crucial in many manufacturing processes.
Applications of Precision Injection Molded Plastics
The applications of precision injection molded plastics are vast and varied. Industries making the most of this technology include:
1. Automotive Industry
In the automotive sector, precision injection molded plastics are used for components such as dashboards, bumpers, and housing for electrical parts. The lighter weight of plastic components contributes significantly to fuel efficiency, making them an attractive option for car manufacturers.
2. Electronics and Electrical Devices
With the continuous advancement of technology, electronics require lightweight yet durable housing. Precision molded plastics help create intricate designs that protect sensitive circuits from damage while providing a sleek appearance.
3. Medical Devices
In the medical field, the requirement for precision and safety is paramount. Precision injection molded plastics are used to create syringes, connectors, and various instruments that adhere to strict regulatory standards.
4. Consumer Products
From kitchen gadgets to toys, many household items are produced using precision injection molding, providing affordability, safety, and durability in everyday objects.
Trends Shaping the Future of Precision Injection Molded Plastics
As technology evolves, so does the field of precision injection molded plastics. Here are some trends that are shaping its future:
1. Sustainable Practices
With increasing concerns about environmental impact, manufacturers are exploring sustainable materials such as bio-based plastics. The integration of recycling processes in production also helps minimize waste.
2. Technological Innovations
The rise of Industry 4.0 brings forth automation and smart manufacturing processes, allowing for precise quality control and efficiency in production. Robotic systems and IoT devices enhance monitoring and response times in molding operations.
3. Customized Solutions
As customer demands become more sophisticated, businesses are moving towards customizable solutions. Precision injection molding technology enables bespoke designs, allowing businesses to meet unique client specifications rapidly.
Challenges in Implementing Precision Injection Molded Plastics
While there are numerous benefits, challenges remain in the adoption of precision injection molded plastics. Some challenges include:
- Initial Investment: The cost of high-quality molds and machinery can be prohibitive for smaller manufacturers.
- Material Limitations: Not all plastics are suitable for all applications, which may limit design options or necessitate compromises in performance.
- Knowledge and Training: Ensuring that personnel are adequately trained in the latest techniques and technologies is vital for maintaining production standards.
Conclusion: The Bright Future of Precision Injection Molded Plastics
As industries continue to evolve in complexity and innovation, precision injection molded plastics will undoubtedly play a pivotal role in shaping the future of metal fabrication. With a combination of efficiency, versatility, and high-quality results, these advanced materials offer myriad possibilities for manufacturers eager to stay ahead in a competitive landscape. Embracing this technology will not only drive business success but also contribute to sustained growth and innovation across sectors.
For businesses looking to leverage the advantages of precision injection molded plastics, partnering with a trusted provider such as DeepMould.net is essential. By investing in this technology, businesses can unlock new levels of quality and efficiency, ensuring they meet the demands of a rapidly changing market.