Understanding Plastic Injection Manufacturing
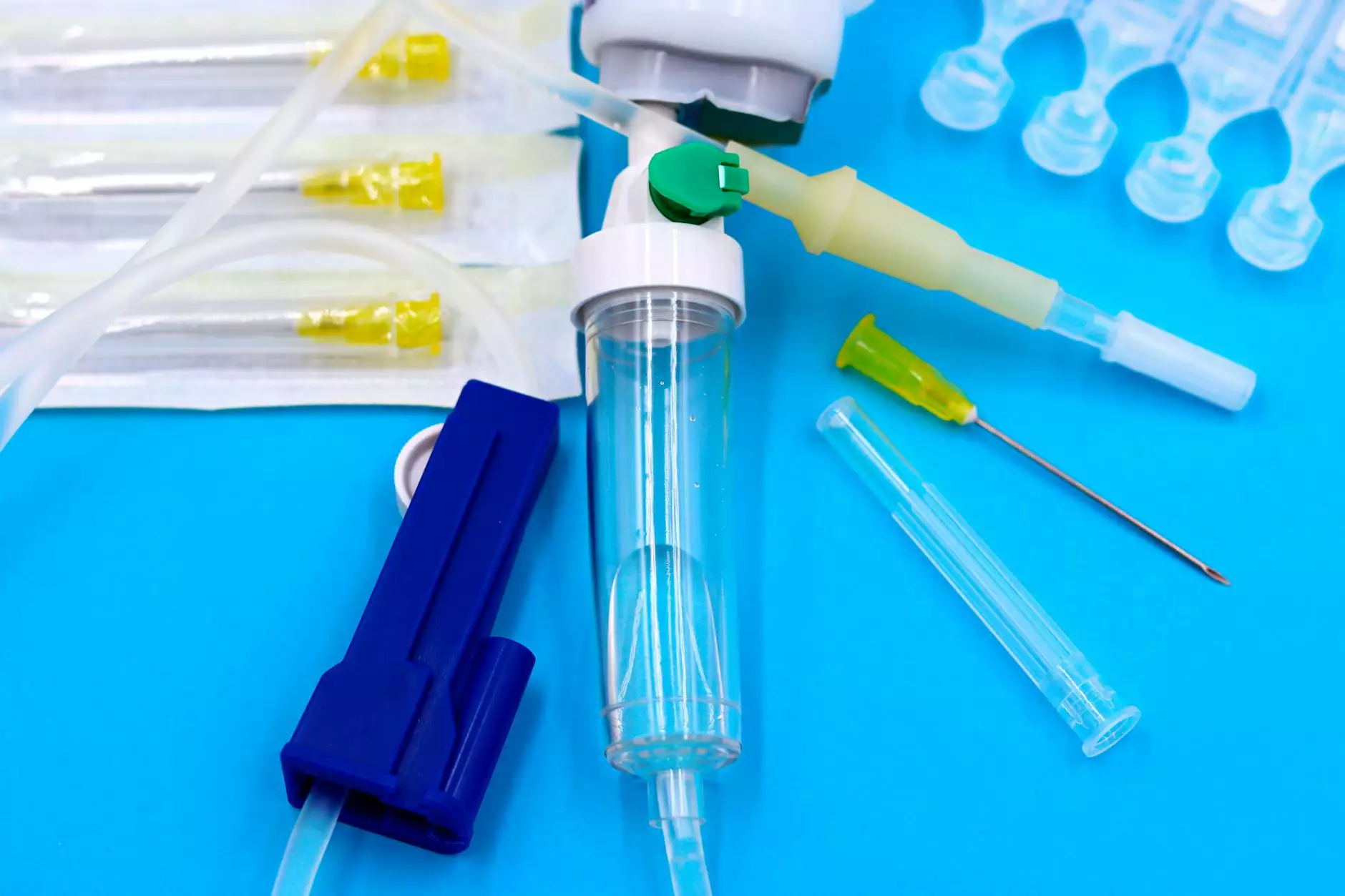
In today's rapidly evolving industrial landscape, the role of a plastic injection manufacturer is pivotal. This process not only serves a wide variety of industries but also plays an essential part in the development of consumer products that we use every day. In this comprehensive guide, we delve deep into what plastic injection manufacturing entails, its advantages, the technology involved, and its future prospects.
What is Plastic Injection Manufacturing?
Plastic injection manufacturing is a process used to produce parts by injecting molten material into a mold. This method enables the creation of intricate designs and complex shapes, making it a vital component in various sectors such as automotive, consumer goods, electronics, and healthcare.
How Plastic Injection Manufacturing Works
The plastic injection molding process involves several key stages:
- Design: The process starts with the design of the part, often using CAD (Computer-Aided Design) software. Engineers create a 3D model that meets specific requirements.
- Mold Creation: After the design is finalized, a mold is created, usually from steel or aluminum. This mold can be quite expensive, but it is crucial for mass production.
- Material Selection: The next step involves choosing the appropriate thermoplastic material, based on the physical properties desired for the final product.
- Injection: The selected plastic is heated until it melts and is then injected into the mold under high pressure.
- Cooling: Once the molten plastic fills the mold, it is cooled to harden the material, taking only a few seconds to several minutes, depending on the part's size and complexity.
- Mold Opening: After cooling, the mold is opened, and the newly formed part is ejected.
- Finishing: In many cases, the part undergoes secondary operations such as trimming, painting, or assembling before reaching the end-user.
Advantages of Plastic Injection Manufacturing
Choosing plastic injection manufacturing offers several competitive advantages:
- High Efficiency: This process allows for high-volume production, making it ideal for parts that are needed in large quantities.
- Cost-Effective: While the initial investment in molds is significant, the per-part cost decreases significantly at high volumes.
- Flexibility: With the extensive variety of plastics available, manufacturers can select materials that provide optimal performance for the part’s intended use.
- Complex Geometries: The injection molding process enables the production of complex shapes that would be challenging or impossible to achieve with other manufacturing methods.
- Reduced Waste: Plastic injection produces less waste than traditional manufacturing due to precise material usage.
The Role of Technology in Plastic Injection Manufacturing
The evolution of technology significantly influences plastic injection manufacturers. Technologies such as:
- 3D Printing: Used for prototyping molds, helping to reduce development time.
- Robotics and Automation: Enhancing the efficiency of operations and reducing the likelihood of human error.
- Advanced Materials: Development of new thermoplastics with improved properties, allowing for more specialized applications.
These advancements contribute to a competitive manufacturing environment, enabling firms to produce higher-quality products at lower costs.
Applications of Plastic Injection Manufacturing
The versatility of plastic injection manufacturing is evident in its wide range of applications:
1. Automotive Industry
In automobile production, plastic parts contribute to reduced weight, improved fuel economy, and lower production costs. Components such as dashboards, bumpers, and interior elements are often produced through injection molding.
2. Consumer Products
Many everyday products, from kitchen utensils to toys, are produced via plastic injection molding. This method allows for unique designs and colors, catering to consumer preferences.
3. Electronics
The electronics industry utilizes injection molding for components like casings and connectors, where precision and durability are critical. This ensures that products can withstand daily usage.
4. Medical Devices
In healthcare, precision and sterility are paramount. Plastic injection manufacturing enables the production of intricate medical devices and components such as syringes and surgical instruments.
Challenges Faced in Plastic Injection Manufacturing
Despite its numerous benefits, the plastic injection manufacturing sector faces several challenges:
- High Initial Costs: The expense associated with mold development can be a barrier for smaller companies or startups.
- Material Limitations: While many plastics are available, not all materials are suitable for all applications, limiting some product designs.
- Environmental Concerns: The environmental impact of plastic production and waste management continues to be a significant challenge, prompting the need for more sustainable practices.
The Future of Plastic Injection Manufacturing
As we look ahead, the future of plastic injection manufacturing is poised for innovation and growth:
- Recycling and Sustainability: Increasing focus is being placed on recycling plastics and developing sustainable materials for injection molding.
- Industry 4.0: The integration of IoT (Internet of Things) in manufacturing processes is driving efficiency and better data management.
- Additive Manufacturing: Hybrid methods that combine additive manufacturing with injection molding are emerging, offering even greater flexibility and customizability.
Conclusion
In conclusion, the role of a plastic injection manufacturer is indispensable in today’s manufacturing landscape. From enhancing product design to contributing to economic efficiency, this innovative method holds the key to numerous applications across various sectors. The continued advancement in technology and an emphasis on sustainable practices will undoubtedly shape the future of plastic injection manufacturing, providing endless possibilities for growth and development.
For businesses looking to partner with a reliable plastic injection manufacturer, DeepMould.net stands out as an industry leader. Specializing in metal fabrication and equipped with state-of-the-art technology and expertise, DeepMould is poised to help companies unlock their potential through high-quality plastic injection molded components.