Understanding Plastic CNC Machining
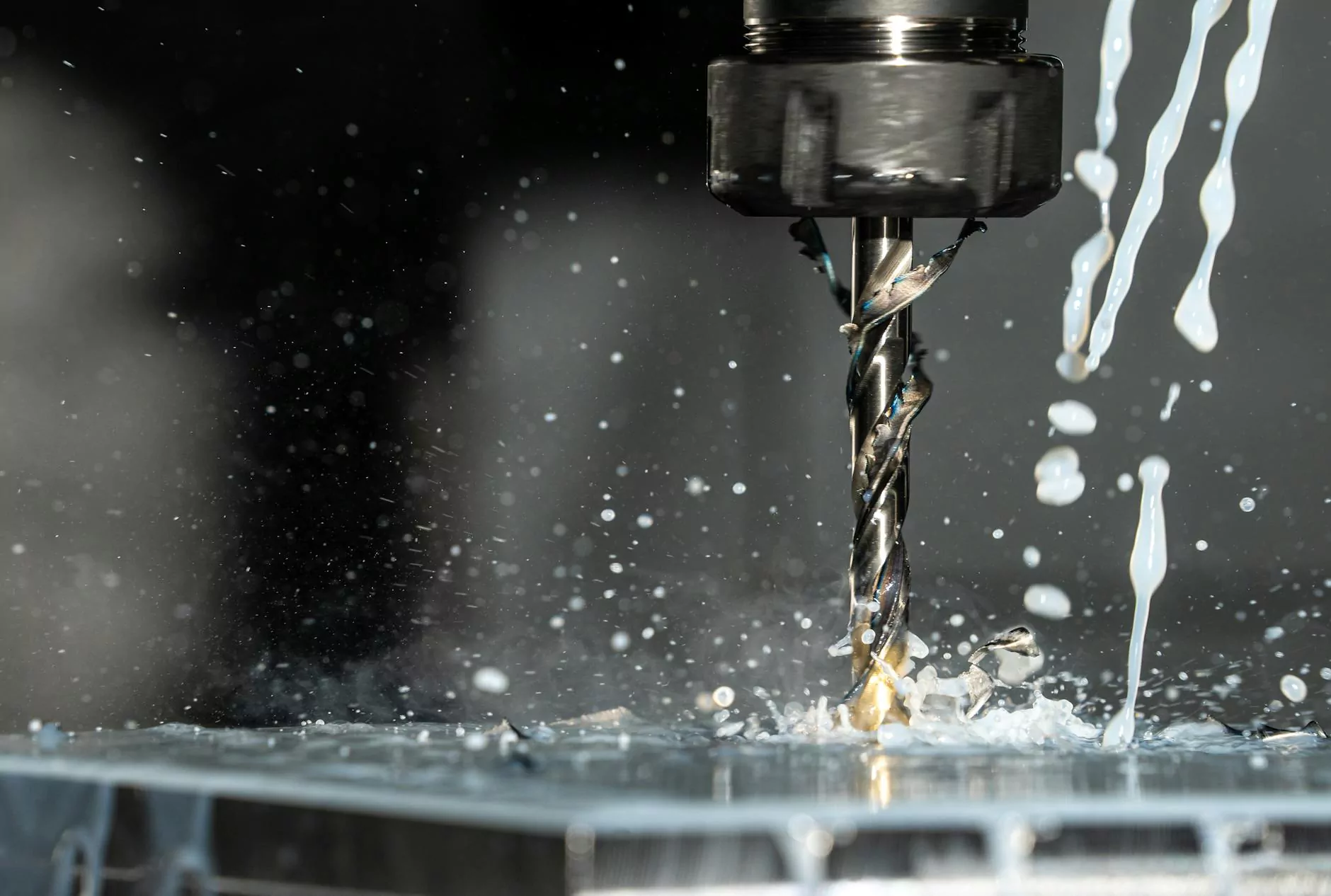
Plastic CNC machining has revolutionized the way industries manufacture crucial components and parts. This precise and efficient technique allows for the creation of intricate designs and helps fulfill various requirements across multiple sectors. As the demand for high-quality plastic components continues to rise, understanding the process and benefits of plastic CNC machining becomes imperative for businesses looking to stay competitive.
What is Plastic CNC Machining?
Plastic CNC machining refers to the automated process of using computer numerical control (CNC) to cut, shape, and create components from plastic materials. It utilizes various cutting tools and techniques managed by a computer program, ensuring unmatched accuracy and repeatability. This process is essential for producing complex geometries and high-tolerance parts that meet industry standards.
Benefits of Plastic CNC Machining
Plastic CNC machining offers numerous benefits that make it a favored choice among manufacturers:
- Precision and Accuracy: CNC machining can achieve tolerances as tight as ±0.002 inches, making it suitable for critical applications.
- Reduced Waste: The process is designed to minimize material waste through optimal cutting paths and techniques.
- Versatility: It works with a wide variety of plastic materials, including acrylic, nylon, polycarbonate, and more.
- Speed: CNC machines can operate continuously, producing components more quickly than traditional machining methods.
- Consistency: Once programmed, CNC machines provide consistent results across large production runs, ensuring uniformity in products.
Applications of Plastic CNC Machining
The versatility of plastic CNC machining allows it to be utilized in various industries, each requiring specific functionalities:
- Aerospace: Lightweight plastic components are vital for aerodynamics, making CNC machining essential in the aerospace industry.
- Automotive: Customized plastic parts such as dash panels, brackets, and housings can be produced efficiently.
- Medical: High-precision components for medical devices and equipment are manufactured using rigorous quality control standards.
- Electronics: Enclosures and connectors made of plastic are produced to safeguard sensitive electronic components.
- Consumer Products: Everyday items like toys or appliances often rely on CNC machined plastic parts for their durability and design.
Why Choose Sumiparts for Your Plastic CNC Machining Needs?
When it comes to plastic CNC machining, partnering with a reliable supplier like Sumiparts is crucial for ensuring quality and efficiency in production. Here’s why:
- Expertise: Sumiparts boasts a team of experienced professionals with in-depth knowledge of CNC machining processes and plastic materials.
- State-of-the-Art Technology: Utilizing advanced CNC machinery ensures optimal performance and the highest quality output for all projects.
- Comprehensive Services: In addition to CNC machining, Sumiparts provides a range of related services including Laser Cutting, Welding, Plastic Injection, and Vulcanized Industrial Supplies.
- Quality Assurance: Commitment to quality is reflected in rigorous testing and adherence to industry standards, ensuring the reliability of all components produced.
- Customization: Every project is tailored to meet specific client needs, ensuring that the final product aligns perfectly with their vision.
The Process of Plastic CNC Machining
The process of plastic CNC machining can be broken down into several key stages:
1. Design and Planning
This initial phase involves creating detailed technical drawings or CAD models that outline the specifications of the parts to be produced. Advanced software is used to simulate the machining process, optimizing tool paths and reducing machining time.
2. Material Selection
Choosing the right plastic material is crucial. Factors such as temperature resistance, impact strength, and chemical compatibility must be considered based on the application requirements.
3. Machining Setup
Once the machinery is programmed with the necessary specifications, the plastic material is set up within the CNC machine, ready for the machining process to begin.
4. Machining Operation
During this phase, the CNC machine follows the pre-programmed paths to cut and shape the plastic material. This is done with high-speed precision and usually involves multiple passes with different tools to achieve the desired finish.
5. Finishing and Quality Control
After machining is complete, components may undergo secondary processes such as sanding, polishing, or surface treatment to enhance their appearance and functionality. Rigorous quality control checks are performed at this stage to ensure each part meets specifications.
Common Myths About Plastic CNC Machining
Despite its advantages, several myths persist about plastic CNC machining. Let’s debunk some of these:
- Myth 1: CNC machining is only for metal materials. Fact: While metal machining is widely known, CNC machining is equally effective for plastics.
- Myth 2: CNC machining is too expensive for small runs. Fact: Depending on setup time and complexity, CNC machining can be cost-effective even for small production runs.
- Myth 3: Plastic parts are less durable. Fact: When manufactured correctly, CNC machined plastic parts can be highly durable and ideal for a variety of applications.
- Myth 4: The quality of CNC machined plastic parts is inferior. Fact: With modern technology and quality assurance processes, the quality of CNC machined plastic parts is outstanding.
Future Trends in Plastic CNC Machining
The future of plastic CNC machining promises exciting advancements that will shape the manufacturing landscape:
- Increased Use of Automation: As technology advances, the integration of AI and machine learning in CNC machining will further improve efficiency and precision.
- Sustainability Efforts: There is a growing trend towards using biodegradable plastics and eco-friendly materials in CNC machining, aligning with global sustainability goals.
- Improved Software: Enhanced CAM software will lead to better simulation and optimization of machining processes, which can significantly reduce waste and improve turnaround times.
Conclusion
In summary, plastic CNC machining is a critical component of modern manufacturing, providing businesses with the ability to produce high-quality, precise, and durable plastic parts efficiently. With a commitment to innovation and quality, Sumiparts stands ready to meet the machining needs of various industries. Understanding the capabilities and benefits of this process is essential for companies looking to enhance their production capabilities and remain competitive in a rapidly evolving marketplace.
If you’re ready to explore the advantages of plastic CNC machining for your business, visit sumiparts.us and discover how our expertise can help you achieve your manufacturing goals.